Hydraulic System Inspections & Maintenance
- Leland Barrow
- Feb 21, 2019
- 8 min read
Hydraulic System Inspections & Maintenance

Hydraulic systems are not as complicated as a person might think. With periodic inspections and preventative maintenance, you can identify components and diagnose potential problems.
All of the components of a hydraulic system have to work together. As a result, damage to one component can lead to damage to other components in the system. For instance, oil overheating, caused by fluid leakage can break down and cause damage to cylinders and the pump. That is why it is important to perform regular maintenance and preventative maintenance inspections to proactively eliminate problems before they occur. A “run to failure” is usually caused by neglect and can be completely avoidable.
A hydraulic system often consists of a pump, hoses and lines, cylinders, motors, valves, a fluid cooling unit, a fluid reservoir, system filters, and hydraulic fluid. The heart of a system is the pump. It uses mechanical energy from the drive engine to pump the fluid and create hydraulic fluid flow and system pressure. Hydraulic Valves control the amount of fluid flow by restricting, bypassing or redirecting it. Cylinders and motors are the muscle and tendons of the hydraulic system. Cylinders have linear, push-pull action while motors use potential energy from the fluid flow to turn the shaft. The speed at which all of these components operate is determined by the hydraulic fluid flow rate, while the system’s hydraulic pressure determines the force that is exerted. The cooling unit cools the fluid and helps maintain a moderate system temperature and the reservoir feeds fluid to the hydraulic pump. Connecting all of these components are hydraulic hoses, lines, and fittings. A failed cooling unit or abnormally high fluid temperatures can cause excessive component wear and accelerate system failure.
Hydraulic Fluid and Filtration
The best process for hydraulic system maintenance is preventing run-to-failures. Keeping contamination out of a hydraulic system will prevent many common problems and catastrophic system failures. Regardless, some contamination is inevitable. Contaminants can enter the system and scratch polished and sealed surfaces. Following these guidelines can help keep your hydraulic system in operable condition and prevent costly repairs.
Actively reduce potential contamination of your hydraulic system. Use clean rags to clean the area around dipsticks, fill plugs and hydraulic filters before removing them. Check or change the hydraulic fluid regularly. Keep all fluid containers tightly sealed when stored and pour hydraulic fluid directly from the container into the system. Avoid using dirty funnels or other devices to transfer fluid from a container to the system.
Perform an initial fluid and filter change after the initial 50 hours of service. The manufacturing process can allow contaminants to enter the hydraulic system. A fluid change after 50 hours will help eliminate contaminants. Change the fluid according to the manufacturer’s schedule as indicated in the owner’s manual.
Check fluid condition and level before each use. Verify that fluid levels are adequate and that the fluid is in good condition. A low fluid level can cause damage to the pump or other system components. If your fluid appears foamy and/or milky, there may be a leak in the system that is allowing air to enter. Air can cause erratic and slow operation of the hydraulic system. Repair any system leaks immediately to reduce contamination and overheating.
Air within the hydraulic system holds some moisture. Water is also a contaminant of hydraulic systems. When the hydraulic system cools down the moisture will condense to water and mix with the hydraulic fluid. Water in the hydraulic fluid will give a milky appearance similar to air contamination. You can confirm that it is water contamination by pouring a 1/8 cup of hydraulic fluid into a metal can and heating it up. If you hear popping or crackling at a high temperature then the fluid has water contamination in it and requires changing.
Regularly check the temperature of the hydraulic fluid during operation. Fluid that is hot to touch, smells burnt or is tacky may be a sign that the cooling system is not working properly or that there are pressure related problems. Inspect the reservoir and system for any dirt, debris or other contamination. Inspect the cooling system for any debris that may inhibit airflow through or around cooling fins.
Hydraulic Pumps
Check pumps for cavitation. Which results from the pump not receiving the proper amount of fluid. Follow these steps to check for pump cavitation.
Look and listen to the pump while the hydraulic system is operating. If the pump rattles then cavitation is occurring and the system should be shut down immediately for repairs.
Check the fluid level and the system filter to determine if there may be restricted fluid flow.
Check lines for any leaks, abnormal bends, and pinching that may restrict flow.
Maintain clean fluid and filters by changing both regularly. Pumps have check valves, vanes, pistons and gears that can be damaged by contaminants. A pump with reduced pumping performance can accelerate the wear of other system components. Hydraulic fluid acts as a lubricant to prevent wear on friction generating components.
Hydraulic Cylinders
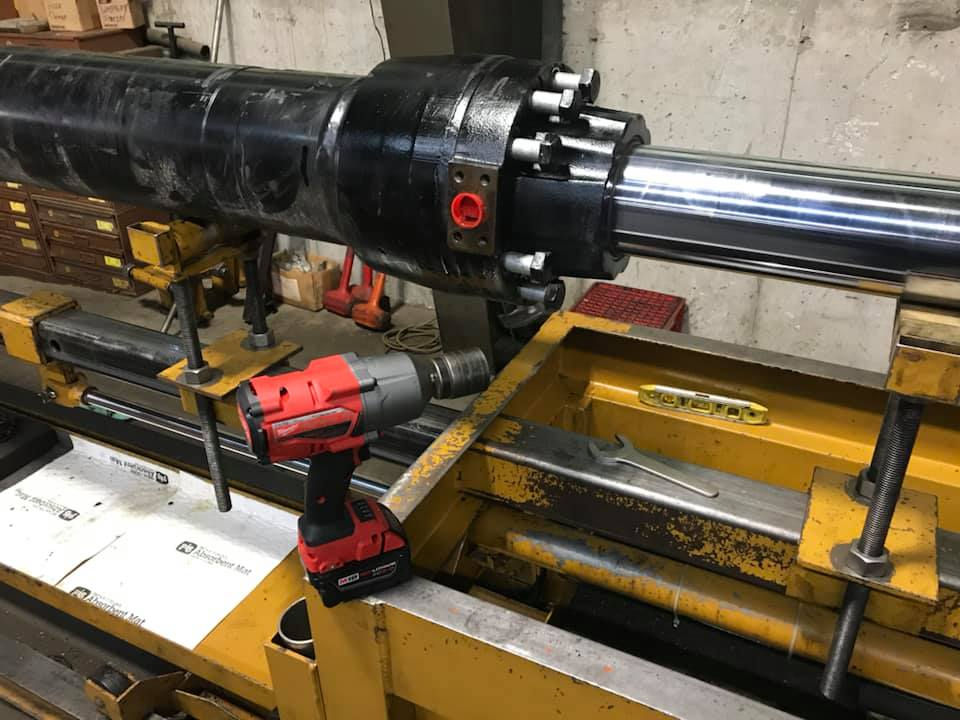
Cylinders have seals and rings that can be damaged by excess pressure and system contamination. A low fluid level can cause damage to polished rods, casings or other areas that have friction. Check the points where the cylinder rod moves in and out of the cylinder housing for leaks. Check cylinder rods for any scratches, scars or other damages that could allow fluid and pressure to leak from the system.
Cylinders are designed to take loads along its horizontal axis only. Verticle loads can decrease cylinder life by causing excess wear on seals and the rod. Hydraulic systems can be tested for breakout force at the cylinders.
Hydraulic Motors
The gears, vanes, and pistons in hydraulic pumps can be scratched and worn by contamination. This can cause system pressure loss. Daily inspections should include checking the drive shaft of the motor for any damage or fluid leakage. Be sure that motors are operating at the correct rpms.
Hydraulic Valves
Hydraulic valves consist of close-tolerance components that open, close or redirect the flow. Valves can be damaged and develop leaks both externally and internally. Leaks will result in low hydraulic pressure within the system. Contaminants can accumulate in valves and restrict system fluid flow.
Other Hydraulic System components
The next aspect of routine maintenance is checking the hoses, lines, fittings, and couplers in the hydraulic system. Inspect all of these components to determine if they have been damaged and for overall condition.
Inspect hoses and lines. Metal lines may be dented from impacts. Inspect lines for cracks, cuts or dents that may restrict flow or cause pressure leaks. Look for improperly crimped hoses, kinked hoses, and collapsed hoses. This can cause reduced system flow and damage components. Hoses can also have internal damage to rubber linings. This can cause pieces of the hose to enter the hydraulic system and contaminate it or restrictions.
Check the hose routing. Sometimes brackets break or hoses were improperly replaced. This can cause hoses and lines to be improperly routed causing problems with system fluid flow. Hoses can be pinched, kinked, overstretched or chafed from improper routing.
Inspect hoses at flex points. Operate the hydraulic system and observe the flex point for kinking or stretching. Often a jerking motion from hoses on system startup can be a sign of localized fluid restrictions.
Check all fittings on hose ends to make sure they are tight. If you notice fluid leaking at a fitting and tighten it. Do not overtighten fittings or thread damage will result.
Check quick connect and disconnect couplings. Always keep the contact points clean. Dirty quick-connect fittings are a significant source of contamination. Cap off couplings when they are not being used. Before connecting any lines, thoroughly clean each coupling.
Keep external components clean of contamination by washing equipment regularly. This will also help to reduce hydraulic fluid temperatures by keeping the cooling system clean.
Make sure that any hose or line replacements are of the same length, size and wall thickness. Refer to the owner’s manual for specifications.
Regular preventative maintenance inspections
It is inconvenient to inspect the hydraulic system before and after each use. Hydraulic systems are often neglected and not inspected until after the operator complains of hydraulic system malfunctions. Often the system has been run-to-failure and it will be too late to prevent a major repair. Aside from regular maintenance described in the owner’s manual, follow these basic procedures every 50 hours or so to determine the health of your system and prevent costly failures. Once you have located a problem, contact a professional to perform the repair work. Professional repair shops can make sure that all of the specifications and tolerances within the system are inspected, maintained and repaired.
Inspecting for restricted hydraulic flow
Slow hydraulics or lack of breakout force is the result of restricted hydraulic fluid flow. Low fluid level, system restrictions, damaged valves, pumps, cylinders, and motors are all possible causes of hydraulic system restrictions.
Operate the hydraulic system and check for which individual hydraulic system components are malfunctioning by operating slowly. For example, if the bucket on a tractor-loader-backhoe does not raise or lower at the normal speed, but other hydraulic attachments operate normally then the restriction is in the lines and components that service the bucket. Visually inspect those components for external leaks. Thoroughly inspect connection points.
If no external restriction is found then the restriction may be internal. Large contaminants or debris may be partially blocking a valve or restricting part of a cylinder or motor.
Check the hydraulic pump, if you cannot isolate the restriction and the entire system is operating slowly. If you hear or feel cavitation then the pump is not getting enough flow and a restriction may be occurring before the pump. Determine that the fluid levels are adequate and the all filters and strainers are clean. Also, check the inlet line to make sure that there is no blockage or kinking. Lastly, verify that the pump shaft is operating and not damaged.
Inspecting for weak hydraulics or breakout force issues
A weak hydraulic system or improper breakout force is the result of low hydraulic system pressure. The system may not be delivering the amount of flow and pressure needed. This may be caused by pressure leaks. Pressure problems can result from damaged pumps, worn valves and worn system components such as motors and cylinders. If, for example, a loading bucket does not lift as much weight as it should, then there is a leak in the fluid system causing pressure to be reduced. To identify the problem follow these steps:
Completely extend the bucket and turn the engine off. Bleed off pressure from the line by moving the control lever back and forth a couple of times. Watch to see if the bucket or arm begins to move as pressure bleeds off. If movement is visible the leak could be in the cylinder, or a valve that controls flow to the bucket, or both.
Support the extended bucket and disconnect the hose that is not under pressure from the cylinder. Now, carefully remove the bucket support. If you see hydraulic fluid seeping from the port then cylinder is leaking. If no leaks are noticed at the cylinder then a hydraulic valve may be malfunctioning.
Repeat this for all attachment points on the hydraulic system. If no leak is identified then the hydraulic pump or one of the primary hydraulic valves may be leaking.
To check that internal leaks are occurring look for excessive heat in the hydraulic fluid. If internal leaks are present the hydraulic fluid will escape where the leak is. Leakage increases friction and causes the hydraulic fluid to heat up.
The initial step in preventative maintenance and preventing run-to-failures is learning about your hydraulic system. Knowing where hydraulic fluid flows and how the system operates is important. Be able to identify hydraulic system components and know how hoses and lines are supposed to be routed. Determine which hydraulic valves service which cylinders and the valves that service the motor. Once you know your hydraulic system and how it operates regular maintenance and preventative maintenance inspections will be easier and more efficient.
I encourage you to develop processes that require your operators to perform pre-operational inspections before using any equipment that has hydraulics. Have a process for recording deficiencies and then getting those deficiencies repaired by a professional hydraulic technician.
תגובות